Every year, a staggering 50 billion shoes flood the market, with the majority meeting their demise in landfills. However, a beacon of hope emerges from the Netherlands, where a company claims to have cracked the code for recycling footwear at a remarkable rate of 2,500 shoes per hour. Major players like Adidas are joining the battle against waste, incorporating materials derived from ocean plastic into their production processes.
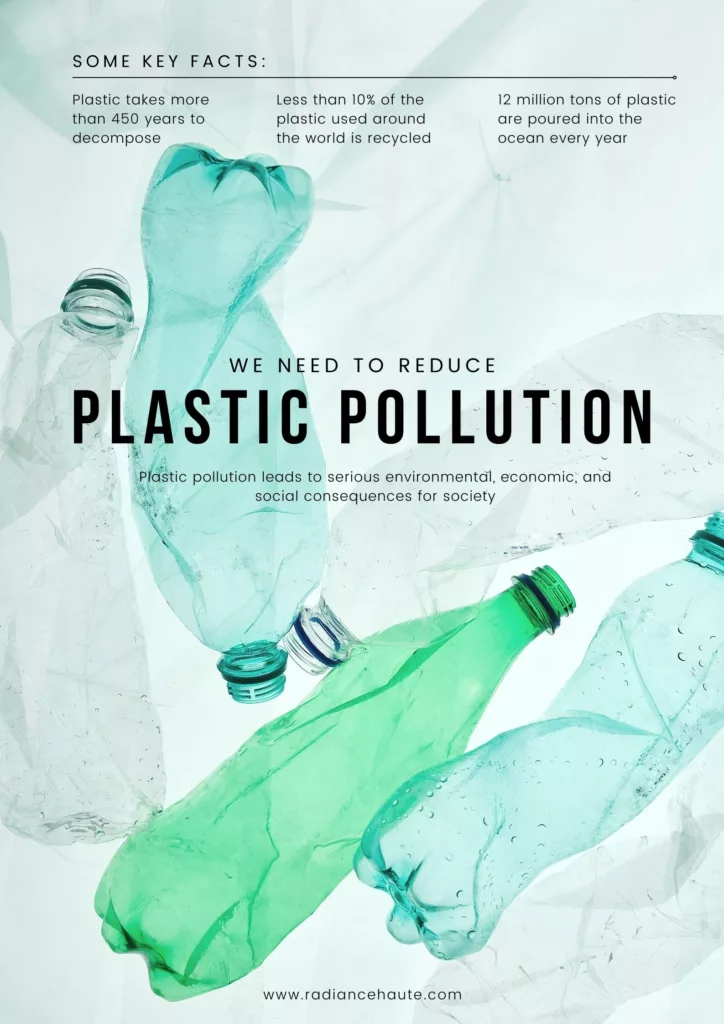
Unraveling the Complexity of Shoe Recycling
Understanding the Shoe Structure
The typical running shoe is a complex assembly of approximately 40 different parts, featuring an array of materials such as plastic, nylon, metal, rubber, and ethylene-vinyl acetate foam. The challenge arises from the formidable glues holding these layers together, making disassembly and recycling an intricate process.
FastFeetGrinded’s Innovative Approach
Enter FastFeetGrinded (FFG), a company founded by entrepreneurs Danny and Erna Pormes. FFG has pioneered an automated mechanical system that circumvents the use of chemical solvents, employing heat and friction to efficiently separate different components. This innovative method ensures the purity of materials, crucial for crafting new shoes.
The Recycling Journey at FastFeetGrinded
- Shoe Intake and Classification
FFG sources shoes from diverse channels, including the Dutch military, collection boxes, and manufacturers. Defective or customer-returned pairs find a purpose through FFG’s recycling process. - Automated Mechanical Separation
FFG’s completely automated system relies on heat and friction, sparing the use of chemicals like glue solvents. The meticulous separation of materials is vital for the success of the recycling endeavor. - Heat-Driven Glue Removal
FFG employs a specialized machine to heat shoes, effectively removing the powerful glues that bind the layers together. This meticulous process ensures the elimination of sticky residue, preventing contamination. - Material Separation and Recycling
The separated materials, including foam and rubber, undergo grinding into tiny particles. FFG also extracts fabric from uppers, transforming it into yarn for new shoelaces, and salvages metals from steel-toed safety shoes. - Founders’ Background and Vision
Originating from their running shop, Runnersworld Hoorn, Danny and Erna Pormes embarked on their recycling journey. Their partnership with Asics exemplifies their commitment to sustainable shoemaking.
Challenges in Recycled Materials
Despite the strides made by FFG and Asics in recycling, limitations persist. High-performance running shoes crafted entirely from circular recycled materials may not match the functional properties of their traditional counterparts.
Global Initiatives: Adidas and Beyond
Adidas, a behemoth producing over 420 million pairs annually, initiated a project in 2015 involving sneakers made from plastic collected from the ocean. However, achieving complete recyclability remains a challenge. The Futurecraft Loop, designed to be recycled into future generations, hinges on customer participation in returning old pairs.
Innovative Materials: Algae-Based Footwear
Researchers at UC San Diego are exploring biodegradable materials, exemplified by an algae-based flip-flop. The simplicity of the process, utilizing algae oil to create flexible and rigid foam components, showcases a potential eco-friendly future for footwear.
Sustainable Entrepreneurship Worldwide
- Turning Landfills into Shoes: Thaely’s Approach
In India, entrepreneur Ashay Bhave founded Thaely, transforming plastic bags and bottles from landfills into shoes. ThaelyTex, a material made without chemicals, signifies a novel approach to sustainable shoemaking. - Creative Reuse: Xclusive International and Mini Soccer Pitches
Companies like Xclusive International creatively repurpose FFG’s materials into displays. In the Netherlands, Willem Tertoole’s company utilizes old shoe materials for mini soccer pitches, offering a second life to discarded sneakers.
Overcoming Adversity at FastFeetGrinded
FFG’s journey has not been without challenges, including a fire that devastated their first recycling plant in 2022. Yet, within a remarkable 10 months, the resilient family had their new facility up and running.
Conclusion
The collaborative efforts of companies like Adidas, Asics, and innovative entrepreneurs worldwide underscore a collective commitment to addressing the global footwear waste crisis. While challenges persist, these endeavors signal a promising shift towards sustainable and environmentally conscious shoemaking.
[…] latest Post […]